Tänapäeval on maailmas kolme tüüpi lehtklaasi: lametõmbeklaas, ujukklaas ja kalandreerimine. Ujukklaas, mis moodustab praegu üle 90% kogu klaasitoodangust, on maailma arhitektuuriklaasi peamine ehitusmaterjal. Ujukklaasi tootmisprotsess asutati 1952. aastal ja see pani aluse maailma standardile kvaliteetse klaasi tootmisel. Ujukklaasi protsess hõlmab viit peamist etappi:
● koostisosad
● sulamine
● vormimine ja katmine
● lõõmutamine
● lõikamine ja pakendamine
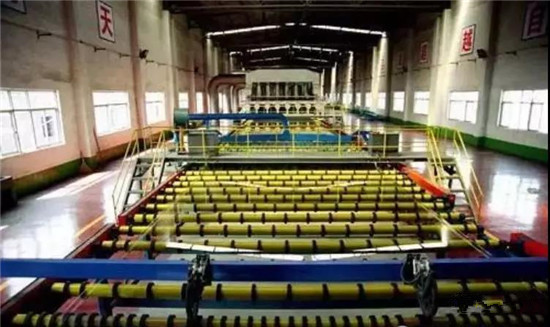
Koostisosad
Partii valmistamine on esimene etapp, mille käigus valmistatakse toorained ette sulatamiseks. Toorainete hulka kuuluvad liiv, dolomiit, lubjakivi, sooda ja mirabiliit, mida transporditakse veoauto või rongiga. Neid tooraineid ladustatakse partiiruumis. Materjaliruumis on silod, punkrid, konveierilindid, šahtid, tolmukogujad ja vajalikud juhtimissüsteemid, mis juhivad tooraine transporti ja partiimaterjalide segamist. Alates hetkest, kui toorained materjaliruumi toimetatakse, liiguvad need pidevalt.
Segukambris transpordib pikk ja lame konveierilint pidevalt tooraineid erinevate toorainete silodest kiht kihi haaval koppelevaatorisse ja seejärel saadab need kaalumisseadmesse liitmassi kontrollimiseks. Nendele koostisosadele lisatakse taaskasutatud klaasikilde või tootmisliini tagastusi. Iga partii sisaldab umbes 10–30% purunenud klaasi. Kuivained lisatakse segistisse ja segatakse partiiga. Segatud partii saadetakse segukambrist konveierilindi kaudu ahju peasilosse ladustamiseks ja seejärel lisatakse söötja abil kontrollitud kiirusega ahju.

Tüüpiline klaasi koostis
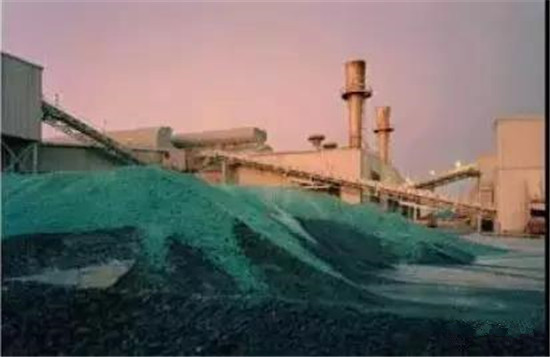
Klaasipuru õu
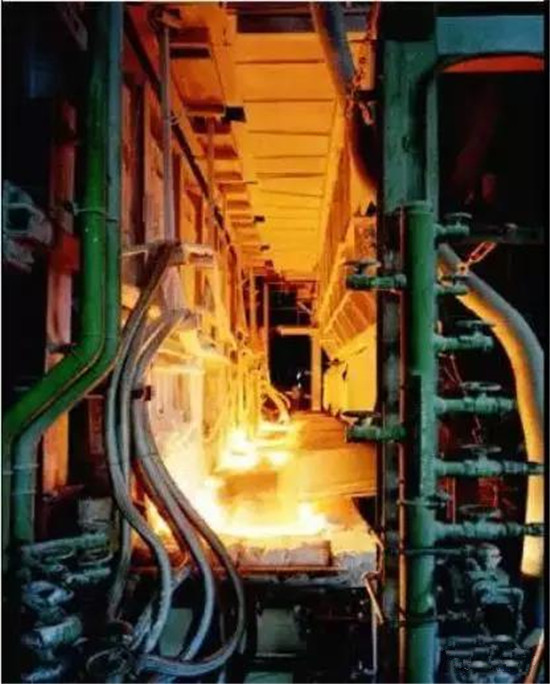
Sööda segatud toorained ahju sisselaskeavasse kuni 1650 kraadini punkri abil
Sulamine
Tüüpiline ahi on kuue regeneraatoriga põikleegiahi, mille laius on umbes 25 meetrit ja laius 62 meetrit ning päevane tootmisvõimsus on 500 tonni. Ahju peamised osad on sulatusbassein/seliti, tööbassein, regeneraator ja väike ahi. Nagu joonisel 4 näidatud, on see valmistatud spetsiaalsetest tulekindlatest materjalidest ja selle välisraamil on teraskonstruktsioon. Segu saadetakse etteande abil ahju sulatusbasseini ja sulatusbasseini kuumutatakse maagaasipihustiga temperatuurini 1650 ℃.
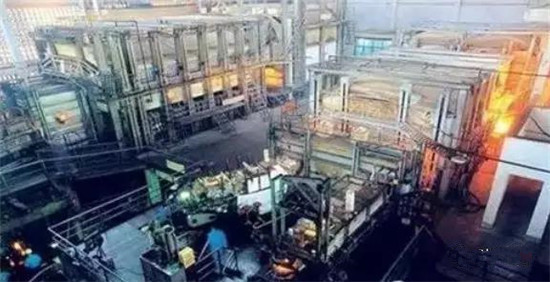
Sula klaas voolab sulatusbasseinist läbi selitaja kaelapiirkonda ja segatakse ühtlaselt. Seejärel voolab see tööosasse ja jahtub aeglaselt umbes 1100 kraadini, et saavutada enne tinavanni jõudmist õige viskoossus.
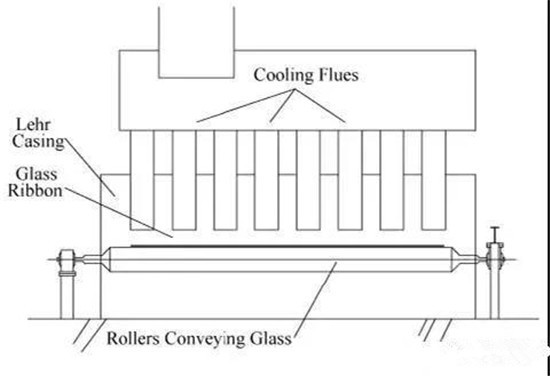
Vormimine ja katmine
Selitatud vedela klaasi klaasplaadiks vormimise protsess on mehaanilise manipuleerimise protsess vastavalt materjali loomulikule kalduvusele ja selle materjali loomulik paksus on 6,88 mm. Vedel klaas voolab ahjust välja läbi kanali ala ja selle voolu kontrollib reguleeritav uks, mida nimetatakse ramiks ja mis on umbes ± 0,15 mm sügavusele vedelasse klaasi. See hõljub sula tina pinnal – sellest ka nimetus ujukklaas. Klaas ja tina ei reageeri omavahel ja neid saab eraldada; nende vastastikune molekulaarne takistus muudab klaasi siledamaks.
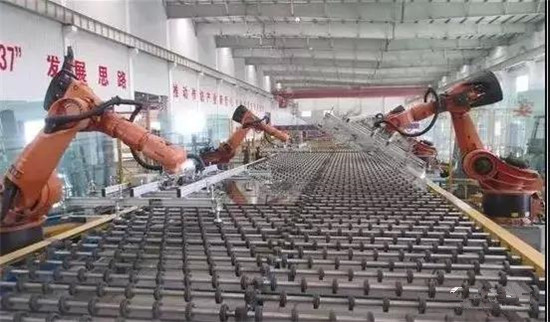
Vann on kontrollitud lämmastiku- ja vesinikuatmosfääris suletud seade. See sisaldab tugiterast, ülemist ja alumist kesta, tulekindlaid materjale, tina ja kütteelemente, redutseerivat atmosfääri, temperatuuriandureid, arvutipõhist protsessijuhtimissüsteemi, on umbes 8 meetrit lai ja 60 meetrit pikk ning tootmisliini kiirus võib ulatuda 25 meetrini minutis. Tinavann sisaldab ligi 200 tonni puhast tina, mille keskmine temperatuur on 800 ℃. Kui klaas moodustab tinavanni sisselaskeava otsas õhukese kihi, nimetatakse seda klaasplaadiks ja mõlemal küljel töötab rida reguleeritavaid servatõmmitsaid. Operaator kasutab juhtprogrammi lõõmutusahju ja servatõmbemasina kiiruse määramiseks. Klaasplaadi paksus võib olla vahemikus 0,55 kuni 25 mm. Ülemise vaheseina kütteelementi kasutatakse klaasi temperatuuri reguleerimiseks. Kui klaasplaat voolab pidevalt läbi tinavanni, langeb klaasplaadi temperatuur järk-järgult, muutes klaasi tasaseks ja paralleelseks. Sel hetkel saab acuracoati kasutada ® peegeldava kile, madal-e-kile, päikesekaitsekile, fotogalvaanilise kile ja isepuhastuva kile otsekatmiseks pürolüüsi CVD-seadmetel. Sel ajal on klaas jahtumiseks valmis.
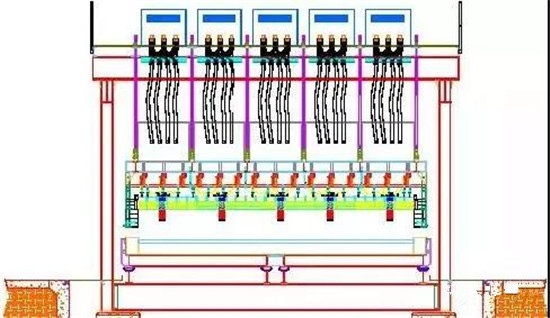
Vanni ristlõige
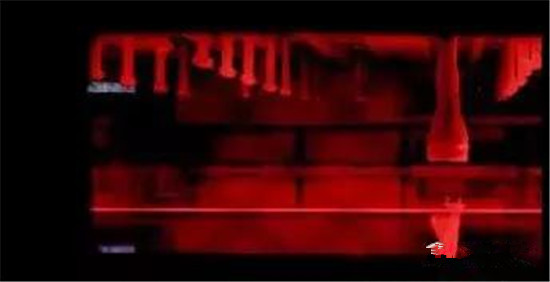
Klaas laotatakse õhukese kihina sulatatud tinale, hoitakse tinast eraldi ja vormitakse plaadiks.
Rippuv kütteelement tagab soojuse ning klaasi laiust ja paksust reguleeritakse servatõmmitsa kiiruse ja nurga abil.
Lõõmutamine
Kui vormitud klaas tinavannist väljub, on klaasi temperatuur 600 ℃. Kui klaasplaati atmosfääris jahutatakse, jahtub klaasi pind kiiremini kui klaasi sisemus, mis põhjustab pinna tõsist kokkusurumist ja klaasplaadi kahjulikku sisepinget.
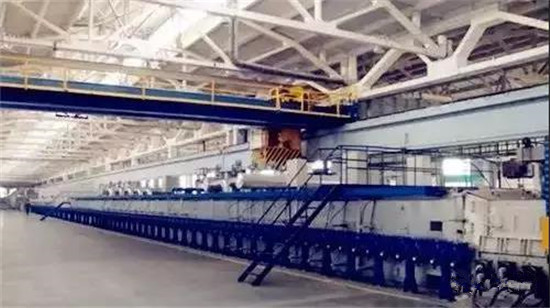
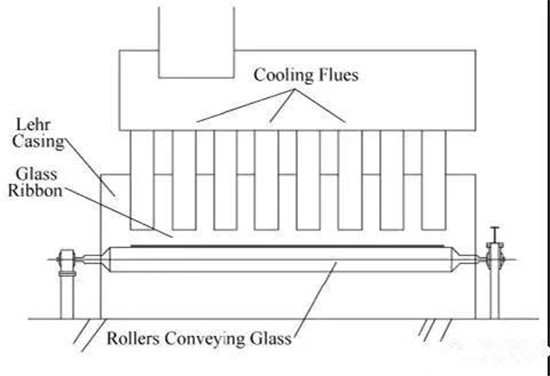
Lõõmutusahju sektsioon
Klaasi kuumutamisprotsess enne ja pärast vormimist on ka sisemise pinge tekkimise protsess. Seetõttu on vaja kuumust reguleerida, et klaasi temperatuur järk-järgult toatemperatuurile langeks, st toimub lõõmutamine. Tegelikult toimub lõõmutamine umbes 6 meetri laiuses ja 120 meetri pikkuses etteantud temperatuurigradiendiga lõõmutusahjus (vt joonis 7). Lõõmutusahi sisaldab elektriliselt juhitavaid kütteelemente ja ventilaatoreid, et hoida klaasplaatide põikisuunaline temperatuurijaotus stabiilsena.
Lõõmutamise tulemusel jahutatakse klaas ettevaatlikult toatemperatuurini ilma ajutise pinge või pingeta.
Lõikamine ja pakendamine
Lõõmutusahju poolt jahutatud klaasplaadid transporditakse lõikealale rulllaua abil, mis on ühendatud lõõmutusahju ajamisüsteemiga. Klaas läbib reaalajas kontrollsüsteemi defektide kõrvaldamiseks ja lõigatakse teemantlõikekettaga, et eemaldada klaasi serv (servamaterjal taaskasutatakse purunenud klaasina). Seejärel lõigatakse klaas kliendi soovitud suuruseks. Klaaspind puistatakse üle pulbrilise keskkonnaga, et klaasplaate saaks virnastada ja ladustada, et need ei kleepuks kokku ega kriimustuks. Seejärel jaotatakse veatud klaasplaadid käsitsi või automaatselt pakendamiseks virnadesse ja viiakse lattu ladustamiseks või klientidele saatmiseks.
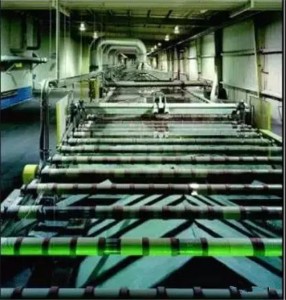
Pärast seda, kui klaasplaat lõõmutusahjust lahkub, vormitakse see täielikult ja viiakse jahutuspiirkonda, et temperatuuri jätkuvalt alandada.